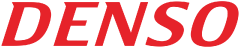
子育てで学んだ、働く上で大切なこと。
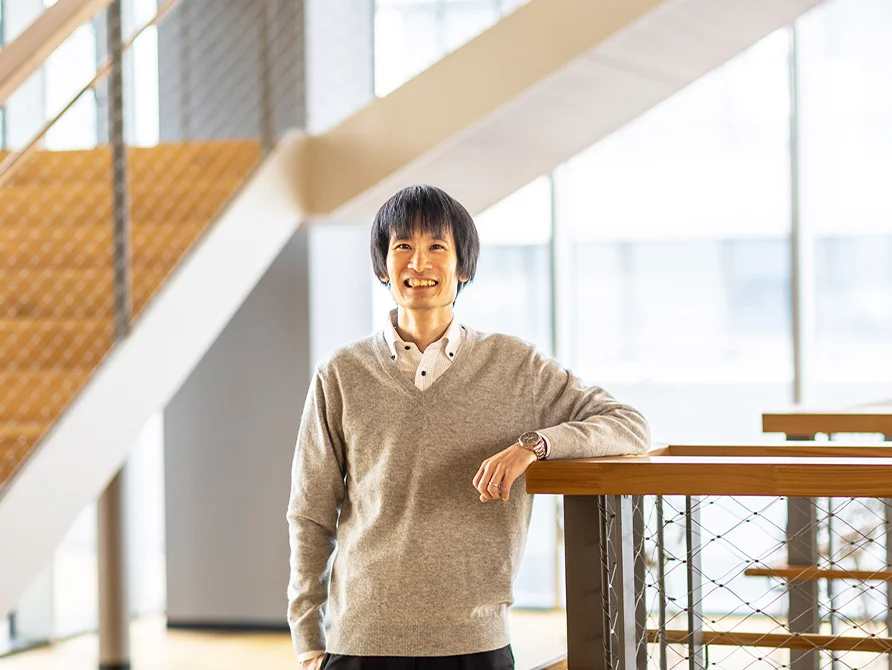
-
-
- 仕事と家庭のバランスを模索している人
- 子育てをしながら働く人
- 男性の育児参加について興味のある人
- キャリアにおける思考の変革を求めている人
- 育児休業の経験について知りたい人
-
-
この記事では、中山清貴さんの経験を通じて、子育てが彼のキャリアや人生観にどのような影響を与えたかを理解することができます。彼は"仕事人間"として仕事を最優先にしていた過去を持ちながらも、育児参加を通じて家族との時間を大切にするようになり、それが彼の働き方や考え方にも変化をもたらしました。具体的には、育児を経験することで、職場でのコミュニケーション方法が変わり、後輩に対する接し方においても相手の立場を考慮するようになったと述べています。また、働く時間の見直しやフレックス制度を活用することでワークライフバランスを模索し、育児と仕事を両立させる取り組みをしていることがわかります。これらの経験から、子どもの存在が仕事だけでなく、より広い社会への貢献に対する意識を高めた点も語られています。
-
-
2024.3.14
キャリア・生き方子育てで学んだ、働く上で大切なこと。
「仕事人間」に起きたパラダイムシフトとは
この記事の目次
-
中山 清貴 kiyotaka nakayama
2012年に新卒入社し、TPS(トヨタ生産方式)にもとづく生産現場の構築や改善推進に従事。現在所属する生産調査部では保全業務のあるべき体制を描き、課題の提起を重ねる。新型コロナウイルスワクチン集団接種会場のレイアウトや作業要領書の作成にも携わり、円滑な運営に尽力。2児の父で、育児休業を計4度取得。
入社12年目を迎え、生産調査部でTPM活動の変革を進める中山 清貴。家庭では2児の父であり、計4度の育休を経て、家族や仕事との向き合い方、さらには人生観までが変わったと言います。自他ともに認める「仕事人間」だった中山や職場に起きたパラダイムシフトとは。
この記事の目次
全社のTPM活動を変革し、設備故障ゼロの製造現場をめざして
──今、携わっている仕事についてお聞かせください。
デンソーグループのすべての製造現場でEF(Excellent Factory:製造体質強化)の思想と行動が浸透するよう、とくにTotal Productive Maintenance(TPM/生産設備の安定稼働に向けた維持管理・改善による原価低減)分野の企画業務を担当しています。TPM活動の変革に向けた全社方針・施策を立案し、各製造現場への展開・支援をしています。
もう少し詳しく話しますと、製造現場において設備故障が起きると、二度と同じことが起こらないようワーキンググループ(WG)を作り、改善(再発防止)を進めます。ただその進め方が会社として標準化されておらず、中には正しく手を打てていない職場もまだまだあります。
その問題に対して、正しい改善の進め方の仮説を立て、自分自身が実際の製造現場で検証します。そこで得た知見や進め方をマニュアルに反映(標準化)し、各製造現場に配布して改善を進めています。これを繰り返すことで、設備故障が起きない製造現場をめざしています。
──過去にはどんな業務をしていましたか。
以前は設備メインではなく、どちらかと言えば人の動きや物の流れに軸を置いた改善活動を、「朝から晩まで現場のど真ん中」でやっていました。他にも、コロナワクチン接種が混みあうことなくスムーズに行えるよう接種会場のレイアウト作りにも携わりました。
「仕事人間」から一転。育休取得を決意し、妻と共に育児に参画
──家庭では2児の父でもあり、育休を取得したとお聞きしました。
長男が生まれた2020年、初めて2週間取得しました。次男が生まれた2023年には1週間、3週間、1カ月と、3回に分けて取得しています。私はかつて「仕事人間」だったので、積極的に育児に参加するようになった変化に自分でも驚いています(笑)。
──もともとは仕事人間だったのですか!?
はい。自他ともに認める仕事人間でした。人生において最優先するべきは、「とにかく仕事をやりきること」だったので、プライベートは二の次。後輩にも同じように厳しく仕事をまっとうするよう求めていましたね。あの時の自分はかなりとがっていたと思います。
──仕事中心の生活が当たり前だったのですね。当時、子どもは好きだったのですか?
実は苦手でした(笑)。当たり前ですが、子どもは意思を伝えるために泣いたり騒いだりしますよね。それに、どう対応してよいかわからなくて……。妻もそれを知っていたので「育児に参加してほしい」とお願いされたことは一度もなく、僕もそこまで育児に関わっている自分が想像できていませんでした。
──正直、驚きです。どのタイミングで中山さんに変化が起きたのですか?
長男の出産に立ち会った時だと思います。いろんな感情があふれて、妻に引かれるほど号泣してしまったんです。新しい生命が誕生したことへの感動や、妻への感謝が芽生え、「生まれることは当たり前じゃないんだ」と思い知らされました。
生まれたばかりの長男と家に帰った際、「めちゃくちゃ、かわいいじゃないか」と感激したのを覚えています。
──立ち会いが大きな転換になり、育休取得に至ったのですね。
この息子と過ごせる時間は今しかない。取らないと絶対に後悔する!と思い、タイミングを見計らって育休も取得し、妻と一緒に育児をしていこうと決意したんです。
子どもとのふれあいで「察すること」を知る。仕事でも相手の立場をより考え行動するように
──ご出産はパラダイムシフトが起きた瞬間でもあったのですね。育児をする上で、普段から意識していることはありますか。
とにかくたくさんの愛情を注ぎたいと思っています。子どもが小さいころに「親が自分を愛している」「必ず味方でいてくれる」と思えたら、強い心が育つのではないかと考えています。質だけでなく、時間もたくさん使って愛情を伝えたいので、毎日ギューッと抱きしめて「大好きだよ」と伝えています。
子どもたちが成長していく中で、僕の愛情が伝わってくれていると嬉しいですし、多少の苦労や挫折も乗り越えられる心の強い子になってほしいですね。
──育休からの復帰後は、仕事でも心境の変化はありましたか。
子どもとのやりとりは、後輩との接し方にも通じると感じました。以前は後輩に対して自分の考えを一方的に伝えていたように思います。具体的に伝えているつもりでも、相手の立場になって、わかりやすく理解できる言葉を選ぶことはできていなかったと思います。
今では後輩の言葉をさえぎらず、共感した上で、相手の立場になって言葉を選んだり、後輩の「やる気スイッチ」はどこにあるのかと考えるようになったりして、マネジメントの仕方も変わってきました。
──今では午後5時になれば退勤するなど、仕事の時間帯も変わったそうですね。
フレックス制度を活用し、5時台に起きて朝早く出社。「絶対に17時までには帰りたい」と宣言し、毎日ではないですが電車内が混む前に帰るように心がけています。達成したいなら口に出さないといけないなと、つくづく感じます。
ただ、制度を利用するからには責任も果たし続けなければいけないと思っているんです。求められるアウトプットはしっかり置いて帰ること。そのあたりは、バランスが大事だと思っています。
──職場にも何かしらの変化が出てきたように感じますか?
時間の制約を意識した私の働き方は、職場にも少しずつ広がっているように感じます。少なくとも私と関わる人は、私の働く時間帯も考慮して会議を開いてくれますし、最近では会社に遅くまでいると「帰らなくていいの?」と気遣ってもらえるようになりました。とてもありがたいと思っています。
世界中の子どもの幸せを願い、募る社会貢献への思い
──ワークライフバランスに対する考え方が変わり、周囲からはどう言われますか。
「言うことや姿勢が本当に変わったよね。まるで別人になったみたい」と上司に言われます。かつての私は仕事中心で、性格もとがっていて、きつい物言いでしたから。
当初ワンオペの育児を覚悟していた妻も、「こんなに育児に参加してくるとは思っていなかった」と驚いていましたね。自分でもここまで変わるなんて、想像もしていませんでした。
──子どもの誕生で、人生におけるやりがいやミッションも変わってきたのではないですか。
かっこいいお父さんでありたい、と思うようになりましたね。今の自分は息子たちから見て、手本となる存在なのかどうか──。そう自分に問い続けていきたいです。そして、かつては生きる意味など考えていなかったのですが、今では「子どもたちを幸せにするために生きているんだよな」と思っています。
そして、最近は、わが子だけでなく、世界中の子どもたちに幸せになってほしいと願うようになり、仕事だけでなく、身近なところでも社会貢献をしたい思いが募ってきました。もともとボランティアや献血はしていたのですが、子どもの誕生をきっかけにより強く意識するようになって。自分がすべきことは何なのかと、いろいろな書籍からも学びを得ながらまさに今、考えている最中です。
自分にできることを見つけ、多くの子どもたちが幸せになるような貢献ができたら、こんなに幸せなことはありません。
※ 記載内容は2023年11月時点のものです
キャリア・生き方執筆:talentbook 撮影:BLUE COLOR DESIGN
COMMENT
あなたが実現したいこと、学びたいこと、可能性を広げたいことに、この記事は役に立ちましたか?
ぜひ感じたことを編集部とシェアしてください。お問い合わせはこちらRELATED
キャリアドリブン 会社という舞台で、自分らしく輝こう- キャリア・生き方2024.1.25 「“17万分の1”でもデンソーを支える大事なピース」 “伝える力”と“聴く力”で現場の生産性を向上させるリーダーの信念
- キャリア・生き方2024.3.5 見えないところで世界を照らす、レーザー加工の技術開発。 学び続けることで、キャリアも人生も豊かにする技術者としての生き様
- キャリア・生き方2023.1.20 若きリーダーの苦悩と成長。 自分と向き合い、相手に寄り添うことで気付けたこと
「できてない」 を 「できる」に。
知と人が集まる場所。デンソーのオウンドメディアDRIVENBASEについて トップページを見る -